An Unbiased View of Die Castings
Wiki Article
Mfg - Questions
Table of ContentsThe 10-Second Trick For Manufacturing IndustriesNot known Incorrect Statements About Hon Hai Precision Some Known Incorrect Statements About Additive Manufacturing The smart Trick of Additive Manufacturing That Nobody is DiscussingThe Main Principles Of Manufacturing
The mould closes and the process repeats. Pre-moulded or machined elements can be inserted into the cavity while the mould is open, enabling the product infused in the following cycle to create and strengthen around them. This process is referred to as Insert moulding and allows solitary parts to consist of multiple products.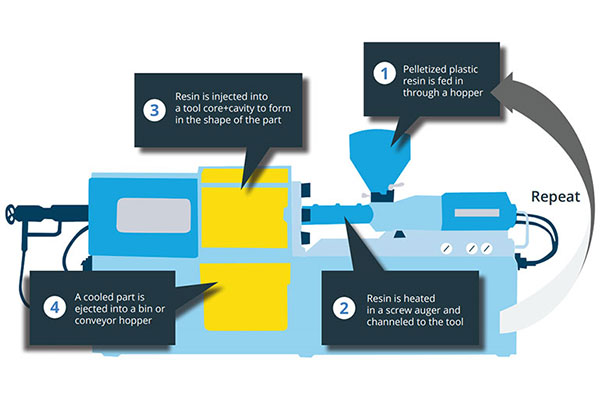
The plastic injection moulding industry has developed over the years from creating combs and buttons to creating a vast array of products for lots of industries consisting of automotive, clinical, aerospace, customer products, playthings, plumbing, product packaging, as well as construction.: 12 Examples of polymers best suited for the procedure [edit] A lot of polymers, occasionally described as materials, may be utilized, consisting of all thermoplastics, some thermosets, as well as some elastomers.
Available materials include alloys or blends of formerly developed materials, so product designers can select the product with the most effective set of buildings from a large selection. Major requirements for selection of a product are the toughness as well as feature required for the final component, along with the cost, however also each material has different specifications for moulding that should be taken into account.: 6 Other considerations when selecting an injection moulding material include flexural modulus of flexibility, or the level to which a product can be bent without damage, along with heat deflection as well as water absorption.
Some Known Questions About Mfg.
Applications consist of buckles for securing as well as disconnecting outdoor-equipment webbing. Equipment [modify] Shot moulding devices include a product hopper, an injection ram or screw-type bettor, and a home heating unit.: 240 Additionally referred to as platens, they hold the moulds in which the parts are shaped. Presses are ranked by tonnage, which expresses the amount of securing force that the maker can put in.

Mould or die are the common terms made use of to describe the device made use of to create plastic components in moulding. Given that moulds have been costly to manufacture, they were normally only used in mass manufacturing where hundreds of parts were being produced. Typical moulds are created from solidified steel, pre-hardened steel, aluminium, and/or beryllium-copper alloy.: 176 The choice of product to develop a mould from is mainly one of business economics; in basic, steel moulds cost even more to build, but their longer lifespan offsets the greater initial price over a higher number of components made prior to wearing.
Facts About Additive Manufacturing Revealed
Shot moulding die with side pulls "A" side of crave 25% glass-filled acetal with 2 side draws. Shut up of removable insert in "A" side. "B" side of die with side pull actuators. Mould design [edit] Typical 2 plates tooling core as well as tooth cavity are inserts in a mould base "household mould" of five different parts The mould includes two primary components, the injection mould (A plate) and also the ejector mould (B plate).Plastic resin goes into the mould through a or gate in the shot mould; the sprue bushing is to secure securely against the nozzle of the shot barrel of the moulding equipment as well as to allow visit homepage liquified plastic to stream from the barrel into the mould, likewise called the cavity.: 141 The sprue bushing directs the liquified plastic to the dental caries pictures through networks that are machined into the faces of the An as well as B plates.
(A) Sprue, (B)&(C)jogger as well as (D)gateways in actual shot moulding product for toys The quantity of resin called for to load the sprue, runner as well as cavities of a mould makes up a "shot". Entraped air in the mould can leave with air vents that are ground right into the parting line of the mould, or around ejector pins as well as slides that are slightly smaller sized than the holes retaining them.
The air can also become so pressed that it fires up as well as melts the bordering plastic material.: 147 To allow for elimination of the moulded component from the mould, the mould functions should not overhang one an additional in the direction that the mould opens up, unless components of the mould are designed to move from between such overhangs when the mould opens up using parts called Lifters.
The 4-Minute Rule for Oem
The coolant absorbs warmth from the mould (which has actually taken in warmth from the warm plastic) and also maintains the mould at a proper temperature level to strengthen the plastic at the most reliable rate.: 86 To ease maintenance and venting, tooth cavities as well as cores are separated right into pieces, called inserts, and also sub-assemblies, additionally called inserts, obstructs, or chase blocks.Much more intricate components are developed using much more intricate moulds. These might have sections called slides, that action right into a tooth cavity vertical to the draw instructions, to form looming part functions. When the mould is additional info opened, the slides are pulled away from the plastic component by utilizing stationary "angle pins" on the fixed mould half. plastic manufacturing.
The part is after that expelled as well as the mould shuts. The closing activity of the mould causes the slides to move on along the angle pins.: see page 268 A mould can produce numerous copies of the same components in a single "shot". The variety of "impacts" in the mould of that part is often inaccurately referred to as cavitation.
In some cases, several cavity tooling molds a series of different components in the exact same device. Some toolmakers call these moulds household moulds, as all the parts are relatede. g., plastic design kits.: 114 Some moulds enable previously molded components to be reinserted to enable a brand-new plastic layer to develop around the first part.
Lean Production - Questions
This system can enable production of one-piece tires as well as wheels. Two-shot or multi-shot moulds are made to "overmould" within a solitary moulding cycle and also have to be refined on specialized shot moulding makers with two or more shot units. This process is in fact an injection moulding procedure done twice and for that reason has a much smaller margin of error.Then the second product, a different colour, is injection-moulded into those rooms. Pushbuttons as well as secrets, as an example, made by this procedure have markings that can not wear away, and stay understandable with hefty use.: 174 Mould storage space [modify] Makers most likely to wonderful lengths to shield custom-made moulds because of their high standard prices.
Report this wiki page